RESOURCES
RESOURCES
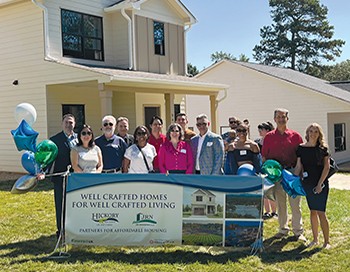
Community Celebrates Success of Affordable Housing Built with Steel Framing Tech
Families in the city of Hickory, North Carolina, are celebrating the speedy completion of new affordable homes in their community. The homes were built quickly using pre-engineered floor, wall and roof systems fabricated from steel by Steel Framing Industry Association member OFFSITEK.
The Charlotte-based integrated construction company uses robots, steel and offsite manufacturing to construct affordable, high-quality homes that are better for the environment, the company says.
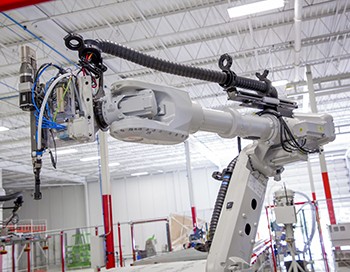
To Robot or Not?
Construction has always been a job for people; workers who pour the concrete, walk the beams, dive the cranes, and put up the walls. People who hammer the nails, place the wires, and plumb the plumbing. Or not.
Manufactured housing is an example of people being more in the supervisory side of construction and machines, including robotics, do the actual building of the roofs and walls, interior and exterior. In some cases, this philosophy is carried all the way to the jobsite.
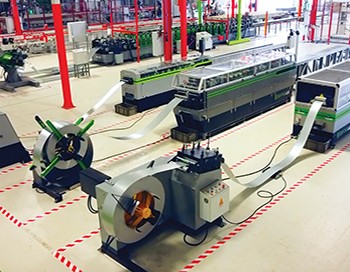
'Time Truly is Money' | Charlotte-based Company Using Robots to Redesign Homebuilding
A new way to build homes has arrived to the Charlotte region. It uses high-tech tools to build a home in an expedited amount of time. OFFSITEK, a Charlotte-based integrated construction company, is using robots, steel, and creative partnerships with local municipalities to give homebuyers options that work within their budgets, are high quality and are better for the environment.
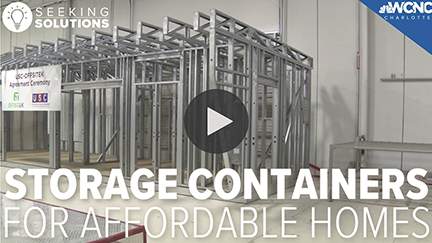
Company Using Robots to Quick-Build Affordable Container Homes
A new partnership between Charlotte-based OFFSITEK and Universal Storage Container will quick-build tiny homes to address affordable housing locally and globally.
Click on the image to watch the video.
Courtesy of WCNC.com
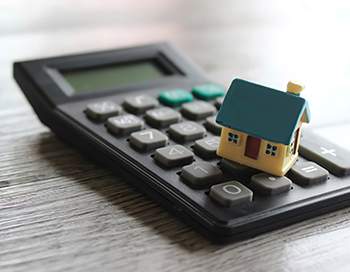
Proposed Partnership Would Use OFFSITEK Steel Framing to Meet Local Housing Demand
Horry County, South Carolina, which includes the city of Myrtle Beach, is exploring a partnership to build steel-framed homes to meet the region’s need for more affordable housing. OFFSITEK, an integrated construction company and SFIA member, recently presented Horry County officials with a plan to build homes for under $200,000.
OFFSITEK, the Charlotte-based integrated construction company, uses robots, cold-formed steel (CFS) and offsite manufacturing to construct affordable, high-quality and eco-friendly homes, the company’s website says.
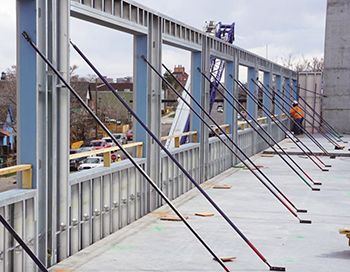
Expert Sources Say Steel Framing is the Ideal Anti-Mold Solution
Mold can be a huge problem in new and existing structures. It can cause structural damage, health problems and even death. Can anything be done to mitigate the appearance of mold in a structure?
Yes. A number of expert sources say that owners and builders should consider using cold-formed steel (CFS) framing for any new or renovation project to help prevent mold intrusion and keep occupants safe.
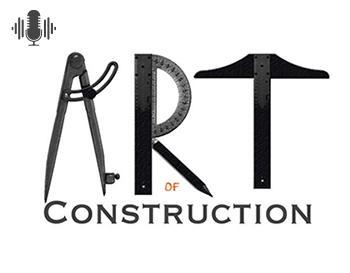
The Key to OFFSITEK Construction is Automation
Art of Construction podcast
Dwight Morgan and Dave Osher, CMO and CEO of OFFSITEK, discuss the history of robotics and automation and why these industries now have their sights set on construction, the forward-thinking business model behind OFFSITEK's factory processes, and why blending skilled labor with robots is the secret recipe for bringing productivity in construction to new highs.
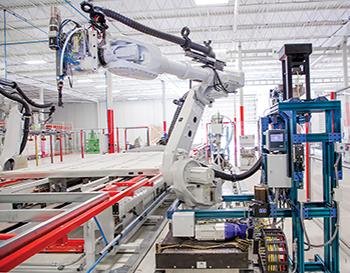
OFFSITEK Partners with Charlotte-Area Municipalities to Deliver Affordable Housing Using Robots and Steel
OFFSITEK, a Charlotte-based integrated construction company, is using robots, steel and creative partnerships with local municipalities to give first-time homebuyers options that work within their budgets, are high quality and are better for the environment.
The City of Hickory, North Carolina, recently announced a partnership to invest in the development and construction of affordable housing on city-owned property.
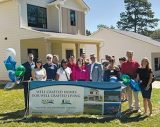
Community Celebrates Success of Affordable Housing Built with Steel Framing Tech
Families in the city of Hickory, North Carolina, are celebrating the speedy completion of new affordable homes in their community. The homes were built quickly using pre-engineered floor, wall and roof systems fabricated from steel by Steel Framing Industry Association member OFFSITEK.
The Charlotte-based integrated construction company uses robots, steel and offsite manufacturing to construct affordable, high-quality homes that are better for the environment, the company says.
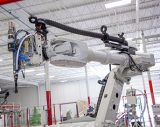
To Robot or Not?
Construction has always been a job for people; workers who pour the concrete, walk the beams, dive the cranes, and put up the walls. People who hammer the nails, place the wires, and plumb the plumbing. Or not.
Manufactured housing is an example of people being more in the supervisory side of construction and machines, including robotics, do the actual building of the roofs and walls, interior and exterior. In some cases, this philosophy is carried all the way to the jobsite.
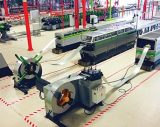
'Time Truly is Money' | Charlotte-based Company Using Robots to Redesign Homebuilding
A new way to build homes has arrived to the Charlotte region. It uses high-tech tools to build a home in an expedited amount of time.
OFFSITEK, a Charlotte-based integrated construction company, is using robots, steel, and creative partnerships with local municipalities to give homebuyers options that work within their budgets, are high quality and are better for the environment.
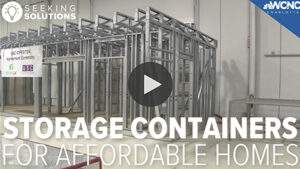
Company Using Robots to Quick-Build Affordable Container homes
A new partnership between Charlotte-based OFFSITEK and Universal Storage Container will quick-build tiny homes to address affordable housing locally and globally.
Click on the image to watch the video.
Courtesy of wcnc.com
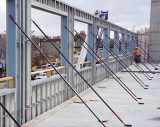
Expert Sources Say Steel Framing is the Ideal Anti-Mold Solution
Mold can be a huge problem in new and existing structures. It can cause structural damage, health problems and even death. Can anything be done to mitigate the appearance of mold in a structure?
Yes. A number of expert sources say that owners and builders should consider using cold-formed steel (CFS) framing for any new or renovation project to help prevent mold intrusion and keep occupants safe.
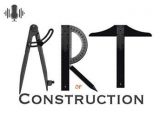
The Key to OFFSITEK Construction is Automation
Art of Construction podcast
Dwight Morgan and Dave Osher, CMO and CEO of OFFSITEK, discuss the history of robotics and automation and why these industries now have their sights set on construction, the forward-thinking business model behind OFFSITEK's factory processes, and why blending skilled labor with robots is the secret recipe for bringing productivity in construction to new highs.
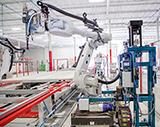
OFFSITEK Partners with Charlotte-Area Municipalities to Deliver Affordable Housing Using Robots and Steel
OFFSITEK, a Charlotte-based integrated construction company, is using robots, steel and creative partnerships with local municipalities to give first-time homebuyers options that work within their budgets, are high quality and are better for the environment.
The City of Hickory, North Carolina, recently announced a partnership to invest in the development and construction of affordable housing on city-owned property.
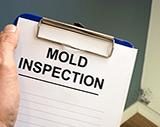
How Cold-Formed Steel Framing Can Help Prevent Mold
Mold growth can be a serious concern for owners and tenants in older buildings — and for good reason. Mold is known to contribute to a variety of health-related issues. What’s discussed less frequently, however, is that mold growth isn’t limited to older buildings. New construction can harbor potentially harmful fungi, too.
To keep future building occupants safe, it’s important to consider the possibility of mold from the beginning of your project and choose a construction material that can help guard against it, such as cold-formed steel (CFS) framing.
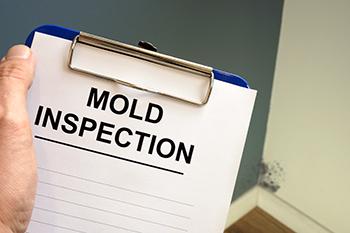
How Cold-Formed Steel Framing Can Help Prevent Mold
Mold growth can be a serious concern for owners and tenants in older buildings — and for good reason. Mold is known to contribute to a variety of health-related issues. What’s discussed less frequently, however, is that mold growth isn’t limited to older buildings. New construction can harbor potentially harmful fungi, too.
To keep future building occupants safe, it’s important to consider the possibility of mold from the beginning of your project and choose a construction material that can help guard against it, such as cold-formed steel (CFS) framing.
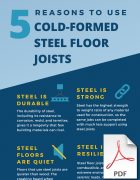
5 Reasons to Use Cold-Formed Steel Floor Joists
Steel delivers a durable and sustainable solution for floor joists. Learn the top five reasons why building professionals prefer steel.
Click on the image for the PDF to learn more.
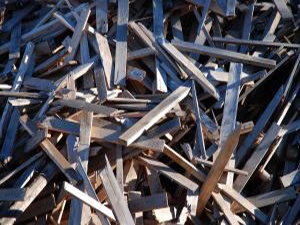
Building Home Value by Reducing Construction Waste
According to a National Association of Home Builders (NAHB) study, an estimated 8,000 pounds of waste is created from the construction of a site built 2,000 square foot home. The majority of that 8,000 pounds is wood, cardboard, and drywall. Almost all of that waste ends up in landfills. Site construction is just inherently inefficient. Materials are dropped and left outdoors in the sun and rain. Framing lumber tends to twist and warp when left exposed for extended periods of time. Materials that are too warped or are too twisted can’t be used in the homes construction and get thrown in a dumpster.
Click on the image for the PDF to learn more.
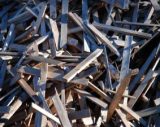
Building Home Value by Reducing Construction Waste
According to a National Association of Home Builders (NAHB) study, an estimated 8,000 pounds of waste is created from the construction of a site built 2,000 square foot home. The majority of that 8,000 pounds is wood, cardboard, and drywall. Almost all of that waste ends up in landfills. Site construction is just inherently inefficient. Materials are dropped and left outdoors in the sun and rain. Framing lumber tends to twist and warp when left exposed for extended periods of time. Materials that are too warped or are too twisted can’t be used in the homes construction and get thrown in a dumpster.
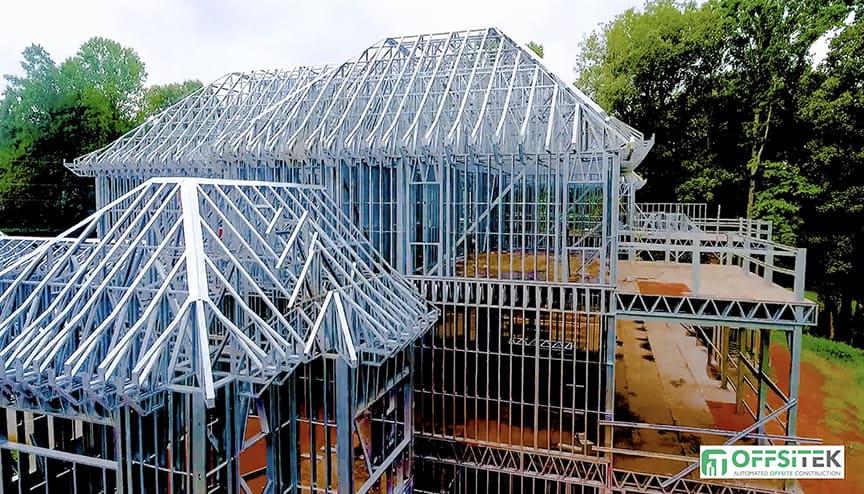
Residential Home in Progress
Watch a drone video of a residential home in progress using cold-formed steel framing.
Click on the image to watch the video.
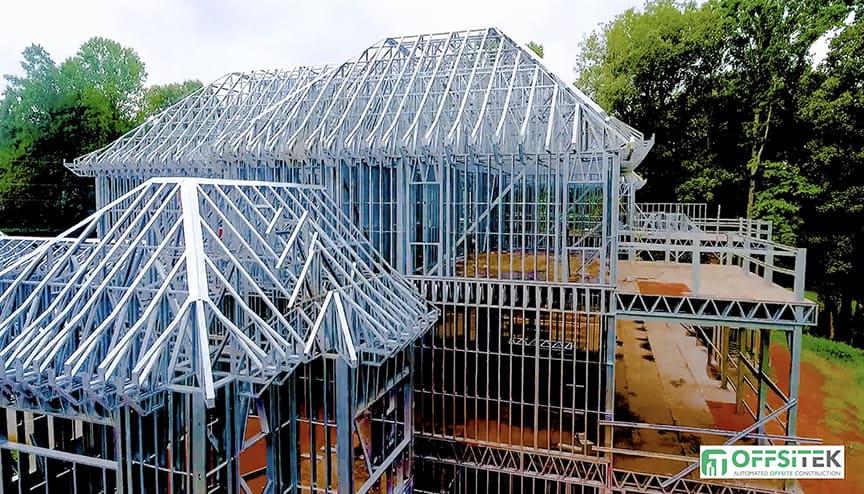
Residential Home in Progress
Watch a drone video of a residential home in progress using cold-formed steel framing.
Click on the image to watch the video.
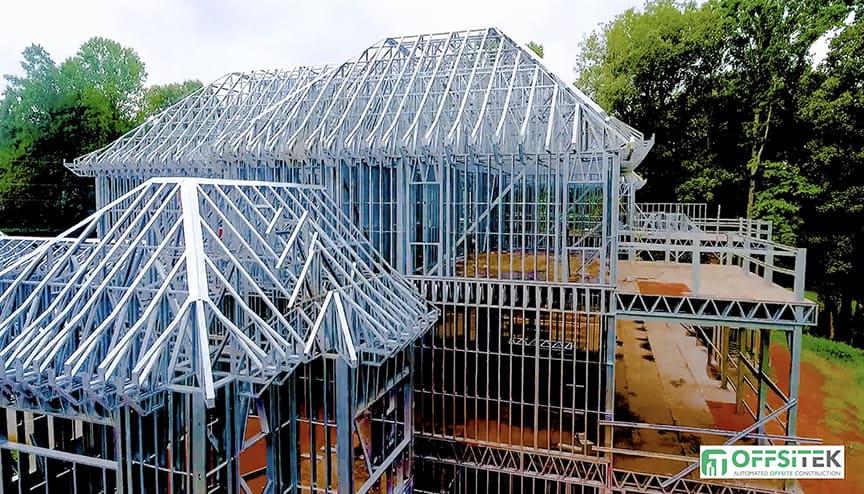
Residential Home in Progress
Watch a drone video of a residential home in progress using cold-formed steel framing.
Click on the image to watch the video.
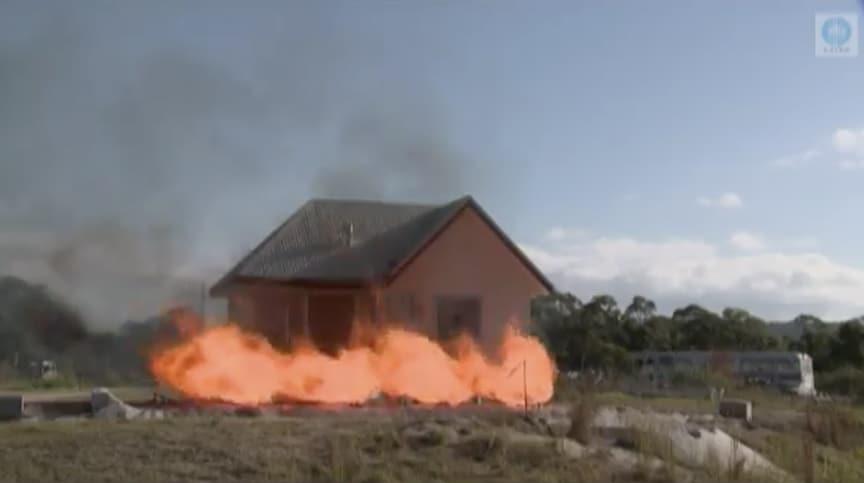
Burning Down the House
Scientists 'flame-test' a steel-framed house to see how the structure would stand up to realistic fire conditions. The house is constructed almost entirely from steel and features a non-flammable roof cavity. It may provide a straightforward and affordable building option for fire-prone areas.
Fire researchers consider that a house constructed predominantly of steel should be able to survive in the flame zone of a real fire assuming the windows or other external openings haven't been breached. The concept is that the entire non-combustable building façade, insulation and frame acts to protect the habitable space.
Click on the image to watch the video.
Courtesy of CSIRO. www.csiro.au/csirovod
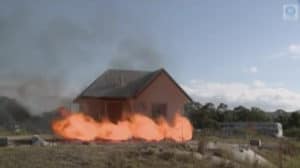
Burning Down the House
Scientists 'flame-test' a steel-framed house to see how the structure would stand up to realistic fire conditions. The house is constructed almost entirely from steel and features a non-flammable roof cavity. It may provide a straightforward and affordable building option for fire-prone areas.
Fire researchers consider that a house constructed predominantly of steel should be able to survive in the flame zone of a real fire assuming the windows or other external openings haven't been breached. The concept is that the entire non-combustable building façade, insulation and frame acts to protect the habitable space.
Click on the image to watch the video.
Courtesy of CSIRO. www.csiro.au/csirovod
10 Ways Cold-Formed Steel Framing Can Lower Your Total Construction Costs
Would you like to cut your construction costs while maintaining work quality and output?
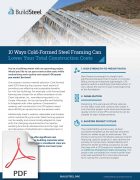
10 Ways Cold-Formed Steel Framing Can Lower Your Total Construction Costs
Would you like to cut your construction costs while maintaining work quality and output?
Click on the image for the PDF to find out how.
Courtesy of BuildSteel.org
Courtesy of BuildSteel.org
Building for Life: the Facts About Cold-Formed Steel & Durability
Here are the facts on CFS durability as you plan your next project.
Click on the image for the PDF to learn more.
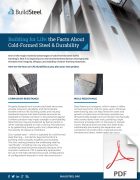
Building for Life: the Facts About Cold-Formed Steel & Durability
Here are the facts on CFS durability as you plan your next project.
Click on the image for the PDF to learn more.
Steel Framing Guide
A builder's guide to steel frame construction.
Click on the image for the PDF to learn more.
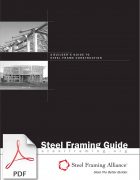
Steel Framing Guide
A builder's guide to steel frame construction.
Click on the image for the PDF to learn more.
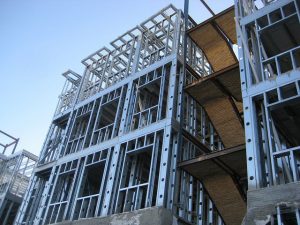
World Steel Association Releases Report on Most Effective Materials for Mid-Rise Construction
The World Steel Association have recently published a report titled Comparative Study of Light Steel Framing, Hotrolled Steel, Concrete and Timber Residential Solutions- Structural Performance. This report aims to provide unbiased information and resources to all stakeholders involved in the construction sector. It details the strong and weak points of various structural solutions using different structural materials within the scope of low-rise (up to 4 storeys) multi-storey residential buildings.
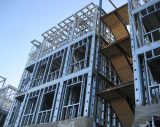
World Steel Association Releases Report on Most Effective Materials for Mid-Rise Construction
The World Steel Association have recently published a report titled Comparative Study of Light Steel Framing, Hotrolled Steel, Concrete and Timber Residential Solutions- Structural Performance. This report aims to provide unbiased information and resources to all stakeholders involved in the construction sector. It details the strong and weak points of various structural solutions using different structural materials within the scope of low-rise (up to 4 storeys) multi-storey residential buildings.
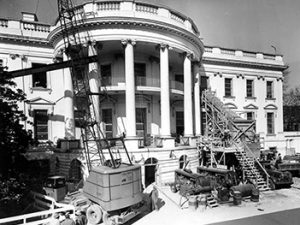
White House Reconstruction
The White House Reconstruction, also known as the Truman Reconstruction, was a comprehensive dismantling and rebuilding of the interior of the White House from 1949 to 1952. A century and a half of wartime destruction and rebuilding, hurried renovations, additions of new services, technologies, the added third floor and inadequate foundations brought the Executive Residence portion of the White House Complex to near-imminent collapse.
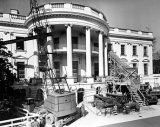
White House Reconstruction
The White House Reconstruction, also known as the Truman Reconstruction, was a comprehensive dismantling and rebuilding of the interior of the White House from 1949 to 1952. A century and a half of wartime destruction and rebuilding, hurried renovations, additions of new services, technologies, the added third floor and inadequate foundations brought the Executive Residence portion of the White House Complex to near-imminent collapse.
704-749-2020
info@offsitek.com
HOME MARKETS ADVANTAGES SERVICES & PRODUCTS CURRENT PROJECTS PRESS RELEASES RESOURCES CONTACT US
©2024 OFFSITEK, LLC. All rights reserved.